När man väljer vilket skärande verktyg som passar bäst för en viss applikation kan det vara svårt att avgöra om ett standardverktyg eller specialanpassat verktyg är att föredra. För att välja rätt måste man beakta en rad olika faktorer, bland annat projektbudget, tidsramar, tillgänglighet, programmeringsbanor, vilken sorts produktion det rör sig om, och ibland även personliga preferenser. Standardverktyg är mycket mångsidiga och passar för tillverkning av en mängd olika komponenter med varierande form.
Dessa verktyg har också en utmärkt prestanda vid bearbetning av olika typer av material. För att produktionsprocessen ska löpa smidigt och utan förseningar är det också mycket viktigt att verktygen levereras i tid. Därför utgör standardverktygen basen i verktygshanteringen ute på verkstadsgolven.
Specialverktygen å andra sidan är konstruerade för att klara specifika arbetsmoment på bestämda komponenter av ett visst material. Syftet med dessa kundanpassade verktygslösningar är att åstadkomma bästa möjliga prestanda vid en specifik bearbetning samt att nå bästa resultat. Nackdelen med denna lösning är att verktyget inte är lika mångsidigt, så det kan vara svårt att tillämpa det till andra bearbetningar än just den det är avsett för. Därför används specialverktyg främst vid massproduktion av stora volymer, särskilt inom bilindustrin.
Specialverktygen finns inte på lager, klara att bara beställas, utan kräver konstruktionsarbete, specialritningar, konceptdesign och samordning med kunden innan de kan gå vidare till tillverkning. Leveranstiden för specialverktyg är därför betydligt längre än för standardverktyg. Verkstäderna står ofta inför ett dilemma när de ska bestämma om de ska välja ett vanligt standardverktyg eller beställa ett specialverktyg som har betydligt längre tillverkningstid. Så frågan kvarstår: vilket verktyg är den bästa lösningen i en given situation? Ska man hålla sig till ett vanligt standardverktyg som går snabbt att få tag på eller välja ett specialverktyg som visserligen gör jobbet betydligt effektivare, men som har avsevärt längre leveranstid? Vid valet måste naturligtvis alla faktorer som påverkar projektets lönsamhet tas i beaktande, bland annat kostnaden per producerad enhet och verktygskostnaderna. Vissa kostnader är lättare att kalkylera för, medan andra, t ex lagerhållningen, är betydligt svårare att förutsäga. När man väljer att använda sig av ett specialverktyg är det därför viktigt att optimera mot den maximala ledtid som krävs för att produktionen ska bli lönsam.
Specialverktygen kan skilja sig åt en hel del beträffande konstruktionens komplexitet. En del kräver bara en enklare modifiering av ett standardverktyg, till exempel en ändring av hörnradien eller verktygslängden. Sådana modifieringar faller under kategorin ”semistandardverktyg” och kan tas fram relativt snabbt. Specialverktygets konstruktionskomplexitet bestäms i en förstudie där man gör en bedömning av kundens tillverkningsbegränsningar samt gör kalkyler över kostnader och produktionstid. Resultaten av förstudien visar produktionens kritiska volym (break-even) och kostnadseffektivitet, dvs. den högre kostnaden och den längre leveranstiden vägs mot tidsvinsten specialverktyget ger vid produktionen. Verktygstillverkarens leveranstider och produktionsberedskap spelar en stor roll för det avgörande beslutet om vilken väg man väljer.
Ett alternativ till specialkonstruerade verktyg är att använda sig av moduluppbyggda verktyg som exempelvis ISCARs MULTI-MASTER (se bild 1) som är roterande verktyg med utbytbara hårdmetallhuvuden. Verktygssystemet MULTI-MASTER innehåller ett stort antal olika verktygshållare (eller skaft som de också kallas), adaptrar, skaftförlängare och reduceringsdelar som gör det möjligt att sätta ihop det specifika verktyg som behövs för att kunna utföra ett visst arbetsmoment.
Additiv tillverkning (AM) har öppnat upp möjligheterna för tillverkning av specialverktyg. Med den här tekniken går det att snabbt tillverka verktyg även med komplex design. Och även om verktygen fortfarande måste slipas för att ytjämnheten ska bli tillräcklig är det fascinerande hur snabbt det går att tillverka produkter med en form som ligger mycket nära den slutliga. Dessutom kan 3D-utskrifter användas för att tillverka hårdmetallskär utan att behöva använda pressverktyg – vilket avsevärt minskar både produktionstiden och kostnaderna. Detta är ett utmärkt sätt att redan under konstruktionsfasen skapa prototyper av skär och producera specialskär i små serier. Det är inte konstigt att den additiva tillverkningen börjar vinna terräng vid tillverkning av hårdmetallskär och -huvuden eftersom metoden gör det möjligt att få snabba leveranser av kundanpassade specialverktyg och specialkomponenter.
Verkstäderna kan snabbt tillverka och anpassa ett specialverktyg om en lämplig lagerhållen standardprodukt inte finns att tillgå. Dock kanske de inte har tillgång till rätt resurser och maskiner för att klara hela tillverkningscykeln. I så fall kan verktygstillverkarna tillhandahålla ”halvfärdiga” verktyg som standardartiklar som kunden sedan själv kan vidarebearbeta och anpassa till den slutliga formen. Dessa halvfärdiga produkter kan vara grovt formade ämnen till verktygshållare, skär och skärhuvuden. En del verktygstillverkare, som exempelvis ISCAR, har dessa i sitt standardsortiment.
I verktygsfamiljen MULTI-MASTER finns extra långa skaft med en inre
MULTI-MASTER-gänga på framsidan och ett centrumhål på baksidan som kan bearbetas och formas av kunden själv. ISCAR introducerade nyligen hårdmetallämnen med två sektioner: en skivformad framsida med ett torx-grepp och en baksida med en yttre MULTI-MASTER-gänga (bild 3). Dessa skärhuvuden har tagits fram för att kunden själv ska kunna tillverka specialverktyg i sin egen verkstad för montering på MULTI-MASTER-skaften och utföra olika bearbetningsmoment som att fräsa spår, gängor, splines, kuggar med mera.
ISCAR har också utökat sitt produktsortiment med ett antal unika ämnen kallade PENTACUT-27. Dessa har fem skäreggar och är tänkta för specialanpassade profiler (bild 4). Dessa stjärnformade ämnen i hårdmetall kan användaren själv slipa till olika former för grund profilbearbetning och spårsvarvning. De kunder som själva tillverkar specialverktyg från ämnen är visserligen få i jämförelse med de som beställer specialframtagna verktyg från verktygstillverkarna. Men när tiden är en viktig faktor ges kunderna på detta sätt ändå möjlighet att ta fram en lämplig lösning inom givna tidsramar. Genom att ge industrin förutsättningar att skapa sina egna specialverktyg ökar vi deras möjligheter att ta sig förbi de hinder de möter i tillverkningen.
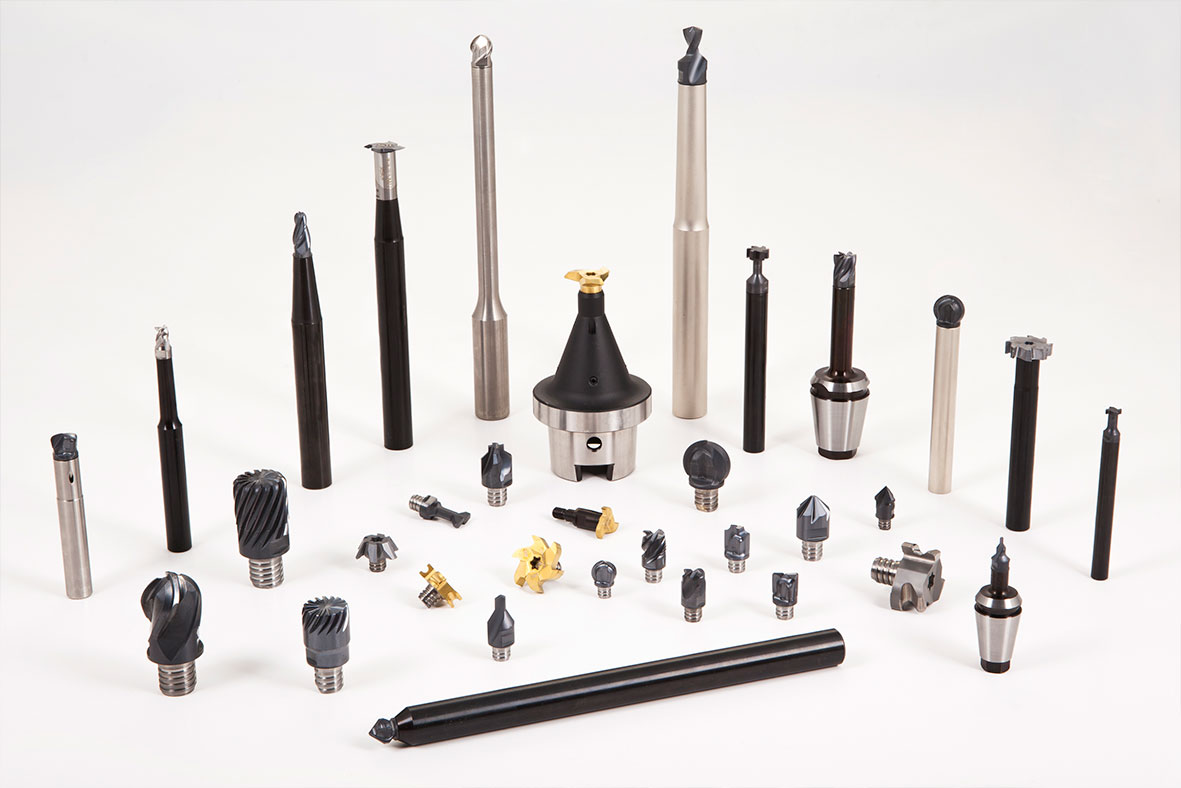
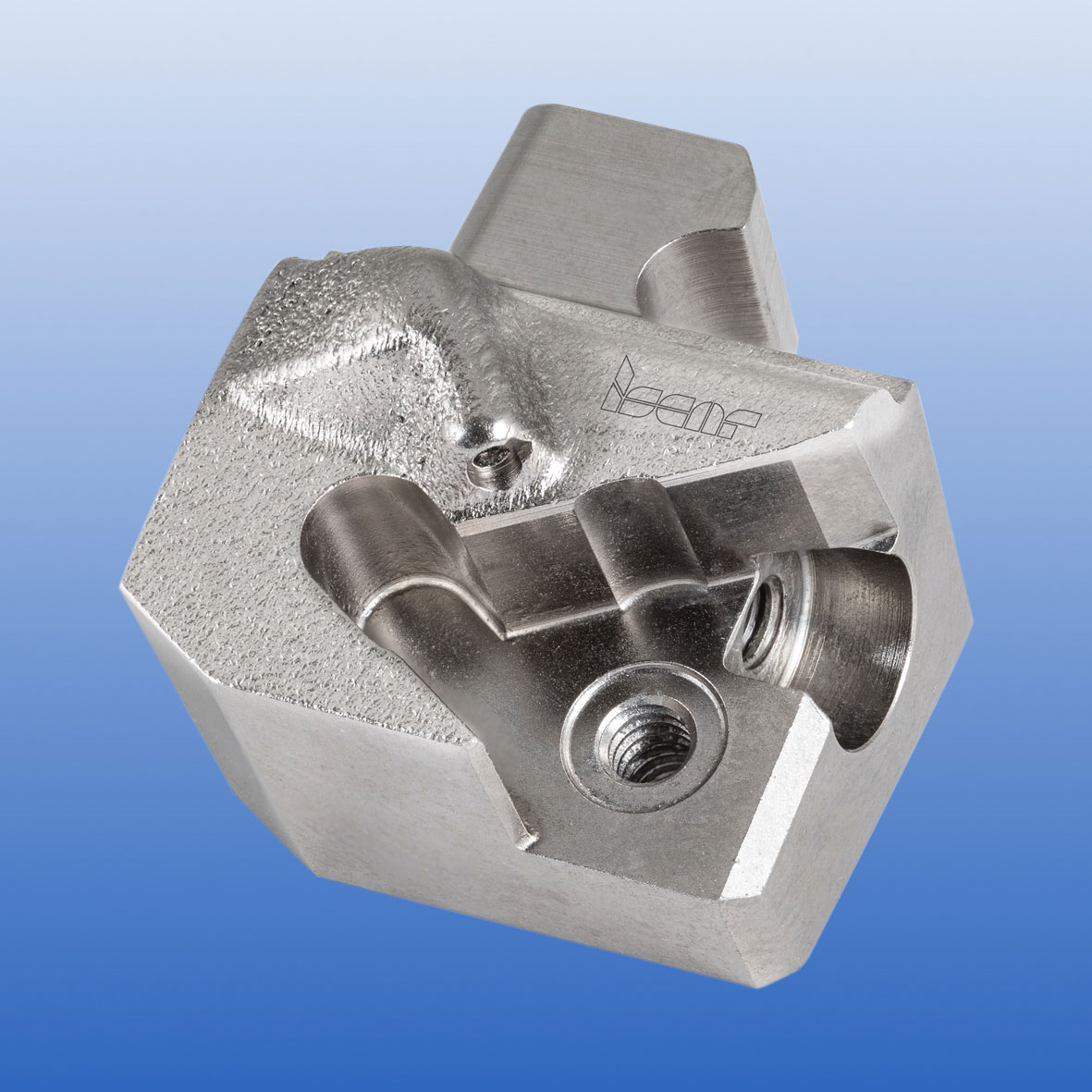
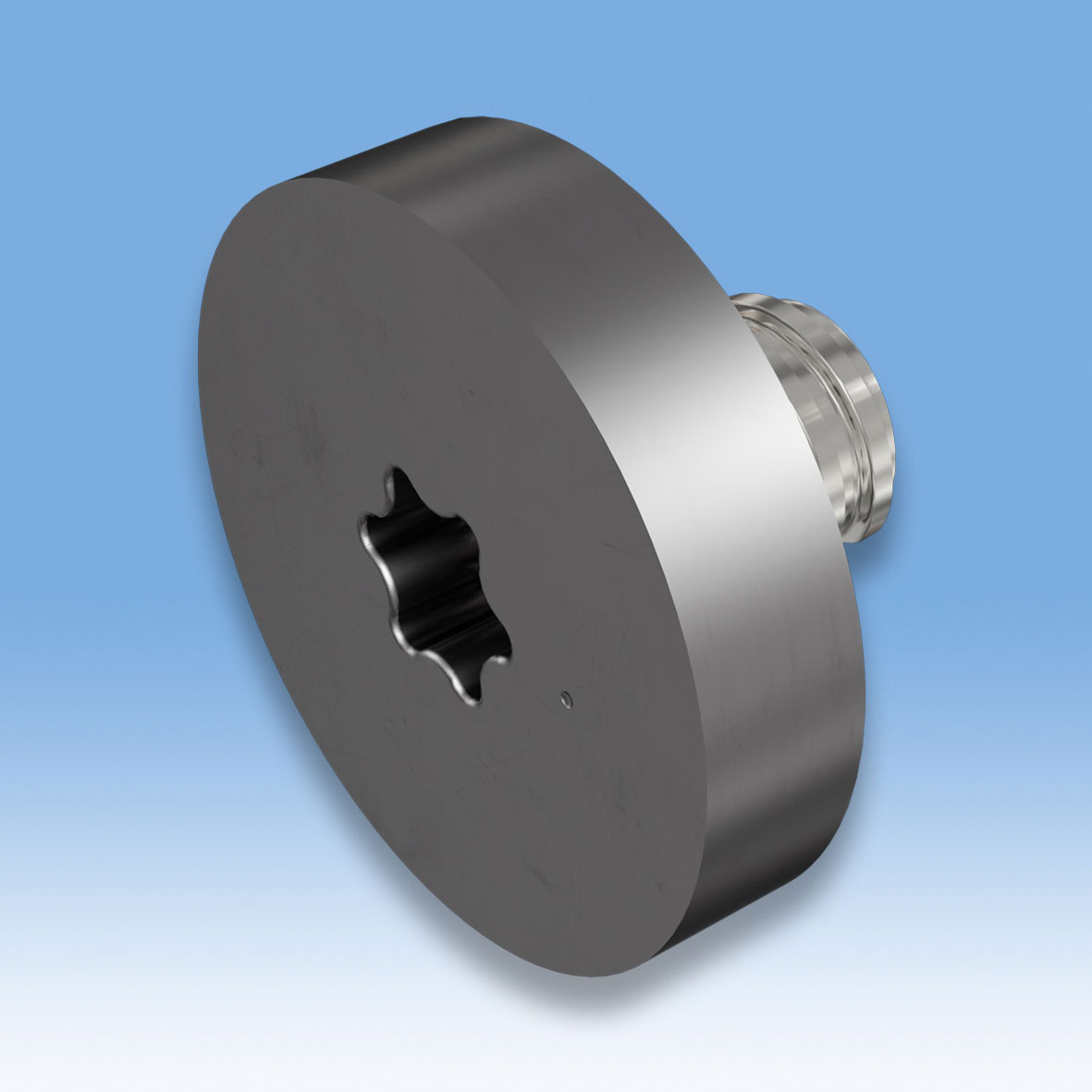
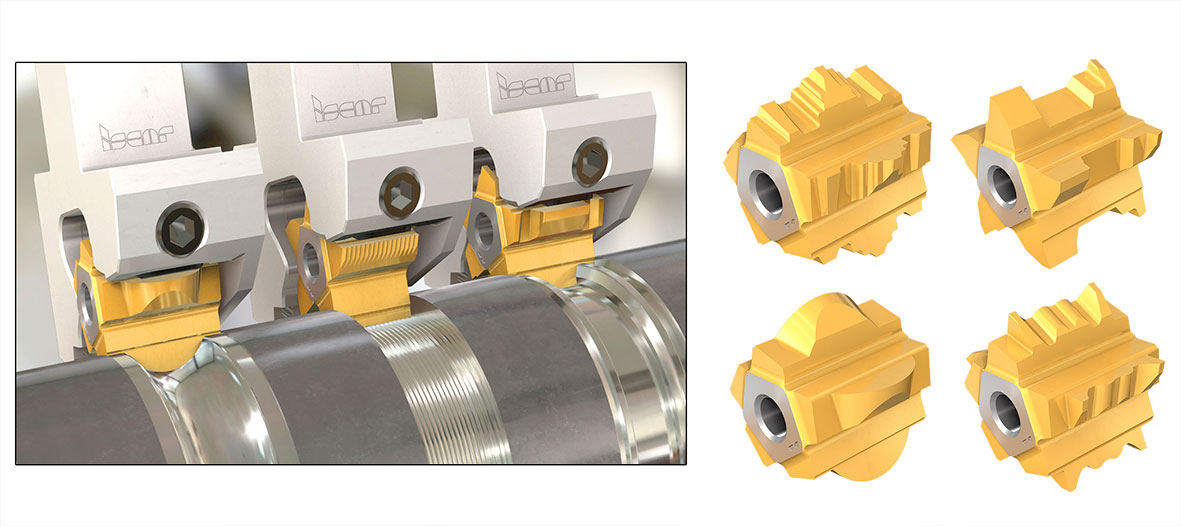